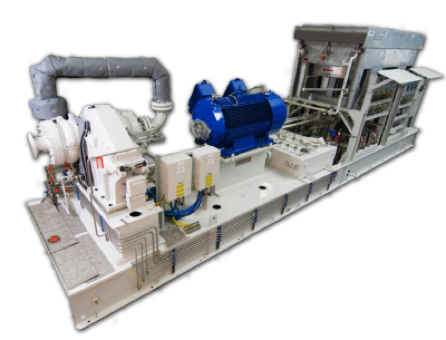
Reliable and economical, Sundyne API 617 / ISO 10439 integrally geared multi-stage compressors
Process gas compressors are the heart of the process. Their reliability directly impacts the productivity and the efficiency of the midstream, hydrocarbon processing or chemical plant.
The Sundyne LF 2000, commonly referred to as a Pinnacle is a compressor that can be outfitted to meet exacting API and ISO standards. The LF 2000 features from one to six stages of centrifugal compressors on a single gearbox. These designs save valuable space and reduces energy costs. Process engineers utilize these multi-stage compressors for midstream, hydrocarbon processing and chemical manufacturing applications including mole sieve dehydration, regeneration of the demethanizer, waste gas, hydrogen recycle and specialty chemical production. Each compressor is custom built to provide pulsation- and vibration-free operation, and to deliver oil-free process gas with zero emissions.
- Flows to 13,000 acfm (22,000 m3/h)
- Maximum working pressure 5,000 psi (350 bar)
Built to meet exacting API-617 / ISO 10439 standards, the LF 2000 will run continuously for 5 to 7 years without costly maintenance or an overhaul. These horizontally configured compressors are ideal for skid packaging — due to their unique modular baseplate — and are easy to install into any process environment. Packaging and instrumentation are customizable to meet your needs and specifications. NACE compliant Sundyne compressors do not rust or corrode.
Sundyne gas compressors provide the performance envelope, the feature set, the reliability ratings and the uncompromising efficiency needed to address the Best Efficiency Point (BEP) for any process gas application in the most demanding environments.
APPLICATIONS
- Mole sieve dehydration
- Regeneration of the demethanizer
- Waste gas
- Hydrogen recycle
- Specialty chemical production
- Fuel gas boost for power generation
Proven to be reliable, safe, compact and efficient, the Sundyne LF 2000 API 617 / ISO 10439 line of integrally geared multi-stage compressors provide a number of operational benefits:
- Up to six stages, overhung, integrally geared compressor per API 617 and ISO 10439 standards
- Single gearbox and motor saves energy and space
- Maximized up time
- Saves space-25% the size of competing reciprocating, barrel, rotary screw and diaphragm compressors
- Continuous operations for 5-7 years with no overhaul
- Optimized compressor engineering to meet the BEP – Best Efficiency Point to save energy through efficiency
- Meets full API 617 and ISO standards for use in hydrocarbon processing or gas processing applications
US 60 Hz
- Maximum Flow 60 to 13,000 ACFM
- Maximum Speed 50,000 rpm
- Maximum Working Pressure 4,000 PSI
- Temperature Range -200 to +500°F
- Maximum Motor Power 10,000 HP
- Reference Standard
- – API-617 for Integrally Geared Process Centrifugal Compressors
- – Other standards on request
- Availability / Reliability
- – 99.7% / 99.8%
- – Up to 7-years uninterrupted operation
- Flanges
- – 18 in. to 2 in.
- – 150, 300, 600, 900# RF standard; other ratings available
- Sealing Technology
- – Dry Gas Seals, Carbon Rings, Labyrinths
- – Single, Tandem or Double arrangement
- – API-692 / API-614 standard compliance available
- Gearbox
- – Integral gearing
- – Horizontal split
- – Gear rating per API / AGMA
- Bearings Technology
- – Thrust: Tapered Land and Tilt Pad
- – Journals: Plain and Tilt Pad
- – Thrust rider rings available on request
- – Start-Up at SOP without depressurization
- Gearbox Lube System
- – Pressurized with filtration and cooling
- – API-614 standard compliance available
- Coupling
- – Low-Speed coupling only is needed
- – Nonlubricated flexible type with spacer
- – API-671 standard compliance available
- Control System
- – Anti-Surge System
- – Performance Control with global or individual controlled processes
- – IGV at one or more stages
- – VFD
- – Suction or Discharge Throttling
- – Intercooling / K-O Drums
- Testing
- – Hydrostatic Test
- – Performance Test as per ASME PTC-10
- – Mechanical Run Test
- – Complete Unit Test (String Test)
- – Additional tests on request
- Packaging
- – From Industry Standard to full API compliance
- – E-Motor or Turbine Driver
- – Enclosures for Noise Attenuation and/or Temperature Control
- – Process Skids
- – Intercooling / KO Drum
- – Modular Arrangement
Metric 50 Hz
- Maximum Flow 100 to 22,000 Am3/h
- Maximum Speed 50,000 rpm
- Maximum Working Pressure 350 bar
- Temperature Range -200 to +500°F
- Maximum Motor Power 7,500 kW
- Reference Standard
- – API-617 for Integrally Geared Process Centrifugal Compressors
- – Other standards on request
- Availability / Reliability
- – 99.7% / 99.8%
- – Up to 7-years uninterrupted operation
- Flanges
- – 18 in. to 2 in.
- – 150, 300, 600, 900# RF standard; other ratings available
- Sealing Technology
- – Dry Gas Seals, Carbon Rings, Labyrinths
- – Single, Tandem or Double arrangement
- – API-692 / API-614 standard compliance available
- Gearbox
- – Integral gearing
- – Horizontal split
- – Gear rating per API / AGMA
- Bearings Technology
- – Thrust: Tapered Land and Tilt Pad
- – Journals: Plain and Tilt Pad
- – Thrust rider rings available on request
- – Start-Up at SOP without depressurization
- Gearbox Lube System
- – Pressurized with filtration and cooling
- – API-614 standard compliance available
- Coupling
- – Low-Speed coupling only is needed
- – Nonlubricated flexible type with spacer
- – API-671 standard compliance available
- Control System
- – Anti-Surge System
- – Performance Control with global or individual controlled processes
- – IGV at one or more stages
- – VFD
- – Suction or Discharge Throttling
- – Intercooling / K-O Drums
- Testing
- – Hydrostatic Test
- – Performance Test as per ASME PTC-10
- – Mechanical Run Test
- – Complete Unit Test (String Test)
- – Additional tests on request
- Packaging
- – From Industry Standard to full API compliance
- – E-Motor or Turbine Driver
- – Enclosures for Noise Attenuation and/or Temperature Control
- – Process Skids
- – Intercooling / KO Drum
- – Modular Arrangement
Castings
- Castings in Carbon Steel, Stainless Steel,
- Ni-Alloys, other materials on request
- NACE and other standards compliance available
- Coatings available for anti-fouling
- Side streams injection or extraction
Impellers
- Fully machined
- Forged 17-4PH SS, Titanium, Ni-Alloys, NACE compliance available
Sundyne LF-2000 Series Integrally-Geared Centrifugal Compressors – PDF
Sundyne Compressor LF-2000 Data Sheet US – PDF
Sundyne Compressor LF-2000 Data Sheet A4 – PDF
Sundyne LF-2000 Compressor Cutaway Poster – PDF
Sundyne Centrifugal Process Gas Compressors – Engineered For Excellence Brochure US – PDF
Sundyne Centrifugal Process Gas Compressors – Engineered for Excellence Brochure A4 – PDF
Sundyne Process Gas Compressors Brochure Russian – PDF
Sundyne MARCA! Com Compressores Centrifugos. Goooool, Portuguese -PDF
Sundyne SCORE! With Centrifugal Compressors. Gooool, Spanish – PDF
Sundyne Fit-for-Purpose Centrifugal Gas Compressors Brochure US – PDF
Sundyne Fit-for-Purpose Centrifugal Gas Compressors Brochure A4 – PDF